In the ever-evolving landscape of textile manufacturing, industrial embroidery machines stand as a beacon of innovation, bringing art and efficiency together in a seamless manner. As more industries integrate embroidery into their production lines, the demand for specialized service and maintenance for these machines has surged. Embroidery machines are intricate devices that require a blend of electrical and mechanical proficiency, alongside an understanding of embroidery software. This article delves into the essential aspects of industrial embroidery machine services, aiming to enhance user experience and ensuring longevity and optimal performance of the machines.
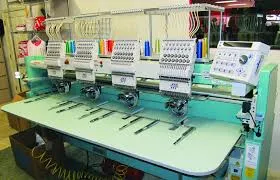
Industrial embroidery machines are integral to the textile industry, powering everything from fashion to home decor and promotional items. These machines are complex pieces of equipment, with numerous moving parts that require regular maintenance and occasional repairs. When not maintained properly, businesses can face downtime, leading to decreased productivity and potential financial losses. Therefore,
having a reliable embroidery machine service partner is crucial.
The first step in ensuring optimal performance of industrial embroidery machines is regular maintenance. This involves routine inspections that should be carried out by trained professionals who possess a deep understanding of the machine's architecture and software. A well-versed service technician will not only clean and lubricate the machine components but will also calibrate the machine to ensure that tensions and pull compensations are set correctly. This prevents thread breakage and ensures high-quality embroidery output.
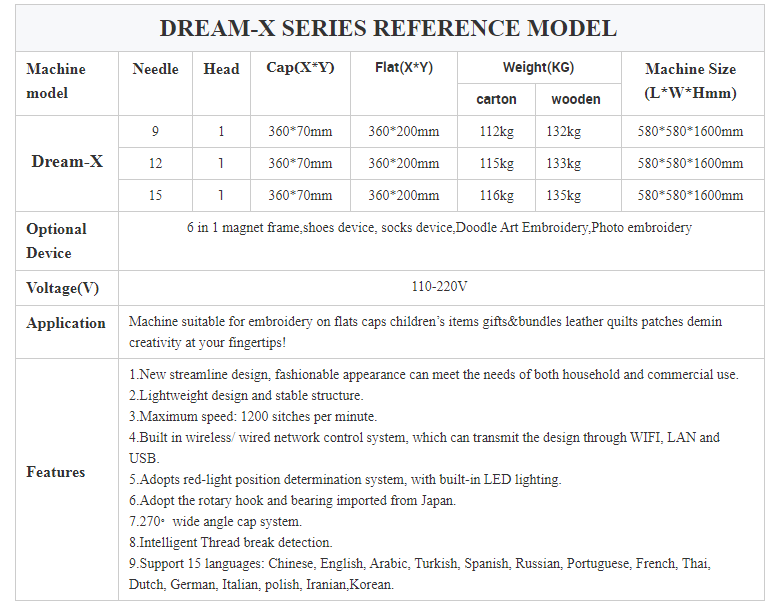
Another critical aspect of embroidery machine service is software updates. Modern embroidery machines are equipped with sophisticated software that controls their operation. As with any software, regular updates are necessary to incorporate new features, fix bugs, and improve security and efficiency. Service providers should offer not only software update services but also training to ensure that operators understand how to utilize new features effectively.
Troubleshooting is an indispensable skill in the realm of embroidery machine service. Machines may occasionally encounter issues ranging from minor thread jams to significant motor failures. A skilled technician can diagnose these issues swiftly, minimizing downtime. This requires a deep understanding of the machine's mechanics and electronics, alongside the ability to decipher error codes and signals. Having a service provider who offers immediate support can dramatically reduce the impact of any machine failures on production.
Aside from regular maintenance and troubleshooting, another component of comprehensive embroidery machine service is the availability of genuine replacement parts. Service providers should stock or have access to a wide range of parts that are needed for various models of machines. This ensures that repairs can be carried out without delay. Additionally, using authentic parts is essential to maintain the machine’s warranty and performance standards.
industrial embroidery machines service
Employee training is an often-overlooked aspect of embroidery machine services. Offering training programs ensures that machine operators are skilled in the basics of machine maintenance and can perform minor repairs or adjustments. This not only maximizes the utility of the machines but empowers workers with skills that enhance their value to the company.
Establishing a preventive maintenance schedule is another key component to optimizing machine performance and lifespan. Preventive maintenance should be part of the service contract and include regular check-ups, necessary adjustments, and proactive replacements of parts that are known to wear out over time. By engaging in preventive approaches, businesses can avoid unscheduled downtimes that are often more costly and disruptive than planned maintenance.
An authoritative service provider will also offer consultation and advice tailored to the specific needs of a business. No two production environments are identical, so the service must adapt to the unique demands of the business’s workflow. Professional consultation helps in understanding how best to integrate the machine into existing production processes, thereby improving overall efficiency and output quality.
The trustworthiness of the service provider is paramount. Businesses should seek reputable providers with verified track records. Looking into testimonials, case studies, and compliance with industry standards can provide indicators of a provider’s reliability. A trustworthy provider will stand by their services, offering warranties and customer support that demonstrate their commitment to ensuring customer satisfaction.
In conclusion, industrial embroidery machine services are not merely about fixing problems when they arise but are about creating a partnership with the service provider that improves machine longevity, efficiency, and output quality. As businesses scale and the demand for embroidered goods increases, investing in comprehensive machine services can lead to a significant competitive advantage. Selecting a service provider that exemplifies expertise, and fosters trust, not only ensures machine reliability but also propels business growth through enhanced productivity and reduced operational hiccups.